تولید لولههای مسی به فرآیندهای پیچیده و دقیقی نیاز دارد که از ذوب مواد اولیه تا شکلدهی نهایی شامل مراحل مختلفی است. این فرآیندها شامل ذوب کاتد مسی در کورههای القایی، ریختهگری مداوم، و نورد پوستههای مسی برای دستیابی به ویژگیهای مورد نظر لولهها هستند. این مراحل به دقت طراحی شدهاند تا کیفیت و دوام لولههای مسی تضمین شود.
پس از تشکیل پوسته مادر، لولههای مسی از طریق کشش سه مرحلهای به شکل نهایی درمیآیند و سپس به صورت کویل، شاخه یا کلاف تنظیم میشوند. فرآیند تنشزدایی به حذف تنشهای باقیمانده کمک کرده و لولهها آماده بستهبندی و حمل به مقصد نهایی میشوند. هر مرحله از تولید به دقت کنترل میشود تا لولههای مسی با استانداردهای بالا و عملکرد مطلوب تولید شوند. آهن وان اطلاعات تکمیلی را ارائه میدهد.
فهرست محتوا
فرآیند تولید لوله مسی
فرآیند تولید لولههای مسی شامل مراحل دقیقی است که هر کدام نقش مهمی در حصول کیفیت نهایی محصول ایفا میکنند. این مراحل به شرح زیر هستند:
- ذوب کاتد در کوره القایی: در این مرحله، کاتدهای مسی به عنوان مواد اولیه در کورههای القایی قرار میگیرند. کورههای القایی با استفاده از میدانهای الکترومغناطیسی، دمای بسیار بالایی را تولید میکنند تا مس به صورت مایع ذوب شود. این مس مذاب به مرحله بعدی فرآیند منتقل میشود.
- ریختهگری مداوم پوسته مادر: مس مذاب از طریق یک شیار مخصوص به پوستهای مقاوم که معمولاً از مواد سرامیکی یا فلزی ساخته شده، ریخته میشود. این پوسته دور لوله مسی را شکل داده و به شکل یک لوله مادر که در مراحل بعدی به کار خواهد رفت، درآمده میشود.
- نورد پوسته مادر و اصلاح کریستالی آن: پوسته مادر مسی که در مرحله قبل تولید شده، تحت فرآیند نورد قرار میگیرد. در این مرحله، مس با استفاده از غلتکهای نورد به ضخامت و شکل مورد نظر درمیآید. همچنین، کریستالهای مس به طور منظمتری تراز شده و اصلاح میشود تا کیفیت نهایی محصول افزایش یابد.
- کشش سه مرحلهای لوله مادر: لوله مادر که در مرحله قبلی به دست آمده، تحت کشش در یک ماشین کشش قرار میگیرد. این کشش به سه مرحله تقسیم میشود که در هر مرحله، ضخامت و قطر لوله تنظیم میشود. این فرایند به بهبود خواص مکانیکی و دقت ابعاد لوله کمک میکند.
- کشش در ماشین دورانی (کویلسازی، شاخهسازی، کلافسازی): پس از کشش، لوله به شکلهای نهایی مانند کویل، شاخه یا کلاف درمیآید. این مرحله با استفاده از ماشینهای مخصوص انجام میشود که به لولهها شکل نهایی مورد نیاز را میدهند.
- تنشزدایی: در این مرحله، لولههای تولید شده تحت تنشزدایی قرار میگیرند. این فرآیند ممکن است شامل استفاده از میدان مغناطیسی یا حرارتی باشد تا تنشهای باقیمانده در لولهها حذف شود و خواص مکانیکی آنها بهبود یابد.
- بستهبندی و حمل: پس از اتمام تمامی مراحل تولید، لولههای مسی بستهبندی شده و آماده برای حمل و نقل به مقصد نهایی میشوند. این مرحله شامل بستهبندی مناسب برای حفاظت از لولهها در طول حمل و نقل و انبارداری است.
این مراحل به دقت و کیفیت نهایی لولههای مسی تاثیر میگذارند و تضمین میکنند که محصول نهایی مطابق با استانداردهای مورد نظر باشد.
استانداردهای طراحی و ساخت لوله مسی
مهمترین استانداردهای مرتبط با لولههای مسی عبارتند از:
- ASTM B88: این استاندارد مشخصات و روشهای آزمون لولههای مسی بدون درز را برای کاربردهای عمومی در فشارهای مختلف تعیین میکند.
- ASTM B251: این استاندارد مشخصات و روشهای آزمون لولههای مسی بدون درز را برای کاربردهای لوله کشی آب و فاضلاب تعیین میکند.
- EN 1057: این استاندارد اروپایی مشخصات و روشهای آزمون لولههای مسی بدون درز را برای کاربردهای مختلف تعیین میکند.
- JIS H3301: این استاندارد ژاپنی مشخصات و روشهای آزمون لولههای مسی بدون درز را برای کاربردهای مختلف تعیین میکند.
این استانداردها به طور کلی شامل موارد زیر هستند:
- مشخصات مواد: نوع مس، ناخالصیهای مجاز و خواص مکانیکی مورد نیاز برای لوله
- ابعاد و ضخامت: قطر خارجی، ضخامت دیواره و تلرانسهای مجاز
- روشهای تولید: فرآیندهای تولید مجاز، مانند اکستروژن یا کشش
- آزمایشات: آزمایشات مورد نیاز برای تأیید کیفیت لوله، مانند تست کشش، تست خم شدن و تست هیدرواستاتیک
- علامتگذاری: الزامات مربوط به علامتگذاری لوله، مانند نام یا علامت تجاری تولیدکننده، نوع لوله، تاریخ تولید و سایر اطلاعات مرتبط
علاوه بر استانداردهای ذکر شده در بالا، دستورالعملها و الزامات دیگری نیز ممکن است توسط سازمانهای محلی یا ملی اعمال شود. برای مثال، در ایران، سازمان ملی استاندارد ایران (ملی ایران) استانداردهای ملی ایران (ISIRI) را برای لولههای مسی تعیین میکند.
در انتخاب لوله مسی مناسب برای یک پروژه خاص، مهم است که استانداردهای مربوطه را با توجه به کاربرد و الزامات پروژه در نظر بگیرید. همچنین، باید از لولههای مسی از تولیدکنندگان معتبر و دارای گواهینامه استفاده کنید.
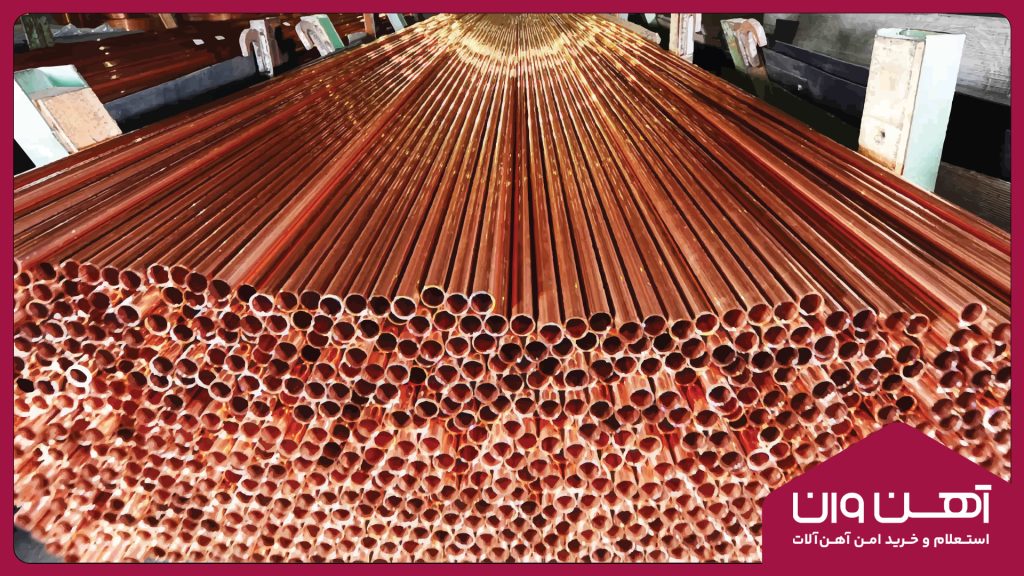
آلیاژهای مورد استفاده در ساخت لوله مسی
آلیاژهای مس به سه دسته اصلی تقسیم میشوند که هر کدام ویژگیها و کاربردهای خاص خود را دارند:
- مس نسبتاً خالص:
– ترکیب: شامل حدود 99 درصد مس و 1 درصد یا کمتر از دیگر عناصر آلیاژی.
– کاربردها: بهطور عمده در تولید لولههای مسی، کابلها و لولههای دو جداره استفاده میشود.
- برنج:
– ترکیب: شامل حدود 95 درصد مس و 5 درصد روی.
– کاربردها: معمولاً در تولید مدالها، فیوزها و لولهها به کار میرود.
- برنز:
– ترکیب: شامل حدود 98.75 درصد مس و 1.25 درصد قلع؛ در برخی موارد ممکن است مقدار کمی فسفر نیز اضافه شود.
– کاربردها: معمولاً برای تولید قطعاتی که نیاز به مقاومت بیشتر و خواص خاص دارند، مانند صنایع ماشینسازی و زیورآلات.
این دستهبندیها بر اساس نسبت عناصر آلیاژی و ویژگیهای فیزیکی و شیمیایی هر آلیاژ تعیین شده است.
معرفی چهار کارخانه تولید لوله مسی در ایران
- کارخانه لوله مسی مهر اصل:
– تاسیس: سال 1369
– مکان: شهرک صنعتی سلیمی، آذربایجان شرقی
– ویژگیها: با مساحت تولیدی بیش از 40 هزار متر مربع، این کارخانه به عنوان بزرگترین تولیدکننده کویل در ایران شناخته میشود. مهر اصل تولیدکننده دستگاهها، قطعات و تجهیزات صنعتی در حوزههای حرارتی، برودتی و تهویه مطبوع است و دارای هفت خط اتوماتیک تولید کویل میباشد. همچنین، این کارخانه به عنوان بزرگترین تولیدکننده داخلی کولرهای گازی صنعتی و خانگی نیز فعالیت میکند.
- شرکت صنایع مس قائم:
– تاسیس: سال 1383
– مکان: شهرک صنعتی مورچه خورت، اصفهان
– ویژگیها: با تجهیزات مدرن برای تولید لولههای مسی، این کارخانه سالانه 24 هزار تن محصول لوله مسی به صورتهای کویل، کلاف، شاخه و شیاردار تولید میکند. محصولات این شرکت از آلیاژهای مسی DHP و ETP با خلوص 99.9 درصد ساخته میشود.
- شرکت صنایع مس باهنر:
– تاسیس: نیمه دوم سال 1370
– مکان: دوازده کیلومتری شهر کرمان
– ویژگیها: این کارخانه بزرگترین مجتمع صنعتی مرتبط با معادن مس و روی کشور است و شامل پنج واحد تولیدی به نامهای ذوب و ریختهگری، نورد، اکستروژن و کشش، سکهزنی و تولید لوله مسی میباشد. کارخانه لوله مسی باهنر از سال 1386 به تولید سالانه 15 هزار تن لوله مسی مشغول است.
- شرکت بابک مس ایرانیان:
– تاسیس: سال 1390
– ویژگیها: این شرکت با آغاز پروژه احداث خط تولید لوله مسی به روش Cast Draw، یکی از پیشرفتهترین روشهای تولید لوله مسی در جهان را به کار گرفته است. این روش با استفاده از تکنولوژی ریختهگری خریداری شده از شرکت UP Cast فنلاند، فرآیند تولید لوله را بهینه کرده و قیمت تمام شده محصول را کاهش میدهد.
این چهار کارخانه با بهرهبرداری از تکنولوژیهای پیشرفته و ارائه محصولات با کیفیت، نقش مهمی در صنعت تولید لوله مسی در ایران ایفا میکنند.
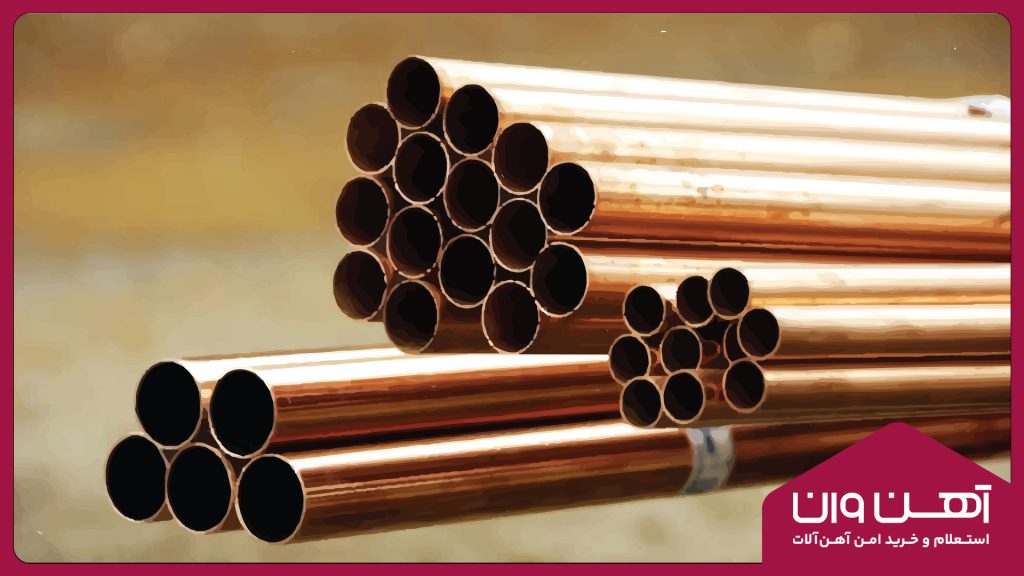
سوالات متداول
مرحله ذوب کاتدهای مسی در کورههای القایی است.
در مرحله ریختهگری مداوم پوسته مادر است.
هدف نورد پوسته مادر، تراز کردن و اصلاح کریستالهای مس است.
مرحله کشش سه مرحلهای لوله مادر است.
فرآیند تنشزدایی است.
مرحله نهایی شامل بستهبندی و حمل لولهها است.
شاید برای شما جالب باشد: تیرآهن 14
جمع بندی آهن وان
تولید لولههای مسی شامل چندین مرحله کلیدی است که هر یک به دقت و با استفاده از تکنولوژی پیشرفته انجام میشود. ابتدا، کاتدهای مسی در کورههای القایی ذوب شده تا مس مایع به دست آید. این مس مذاب سپس به پوستههای مقاوم ریخته میشود تا ساختار اولیه لوله شکل گیرد. بعد از ریختهگری، پوستههای مسی از طریق نورد مورد پردازش قرار میگیرند تا کریستالهای مس به شکل منظمتری تراز شوند. این مرحله به افزایش کیفیت و استحکام لوله کمک میکند.
در مراحل بعدی، پوستههای مسی به وسیله ماشینهای کشش سه مرحلهای به لولههای نهایی تبدیل میشوند، که این فرآیند باعث تنظیم دقیق قطر و ضخامت لوله میشود. سپس، لولهها به شکل کویل، شاخه یا کلاف درآمده و تحت فرآیند تنشزدایی قرار میگیرند تا تنشهای باقیمانده حذف شود. نهایتاً، لولههای مسی بستهبندی شده و برای حمل به مقصد نهایی آماده میشوند، با توجه به استانداردهای بالا و کیفیت مطلوبی که در هر مرحله تولید به دست آمده است.
References
https://www.copper.org/publications/newsletters/innovations/1998/09/howdo_tube.php